第2章 サプライチェーンマネジメントの実践
2.4 SCM展開上の問題と対策
(4)営業と物流の問題
営業活動は、対人関係という不確定な要素を基盤としています。また日本的商習慣がSCMの阻害要因となっている部分もあります。そして物流は地理的な要因が影響します。具体的には次のような問題が挙げられます。
問題1:需要予測
SCMを推進する際に、営業関係で検討されるのは、需要予測についてでしょう。見込み生産だけでなく、受注生産でも、部品や材料を見込みで調達するBTOなどの生産方式をとる場合には、需要予測の精度が在庫量に影響します。需要予測は、過去の売上のトレンドや季節性、業界・マクロ経済の動向、営業前線の情報、キャンペーン等の販促業情報などに基づく予測を、単独あるいは組み合わせて算出することが多いようです。
予測のやり方を見直して精度を上げる努力は必要でしょう。しかしながら過大な期待は禁物です。製品が売れるかどうかは、製品そのものの内容だけでなく、競合製品との優劣、販促の効果、顧客の心・懐具合、営業マンとの人間関係など複雑な要因で決まるのです。精度を向上するには、これらの要因に迫る必要がありますが、今のところこうした複雑な要因と売上を結びつけるメカニズムすらわかっていないのが実情でしょう。
特に新製品の売上予測は困難です。過去の製品のマイナーチェンジならば過去のトレンドを延長すればよいでしょうが、新規の機能・新規のセグメントの新製品については、その需要予測は、桁違いにはずれることもあります。
対策1:生産計画の多サイクル化
需要予測の精度を上げるよりも、生産計画を多サイクル化するほうが、確実に効果が出せます。生産計画を月次で立てているならば、その立案サイクルを旬・週・日と短くします。実際に売れた数によって、前のサイクルで計画した在庫数に対して実際の在庫数が増減しています。計画を立案するときに、その増減を反映します。予測の精度を上げるのではなくて、予測がはずれたことをできるだけ速く次の生産に反映するのです。
計画を立案してから、製品が完成するまでのリードタイムを短くすることも有効です。例えば、ある月の始めに翌月1カ月の生産計画を立てていたとしましょう。それが、週の初めに翌週の生産計画を立てるようにすれば、需要の変動に追随するスピードが上がります。前の日の売上が翌日の生産計画に反映できれば、需要予測の精度はが問題となる商品は極めて少ないでしょう。生産計画の多サイクル化とリードタイムの短縮をやってから需要予測の精度向上に取組むことをお勧めします。
問題2:販売リベート
販売リベートもSCMを推進するときの問題になります。販売リベートといっても様々な形態があります。最も多いのは数量リベートでしょう。顧客との間で、年間の売買量の目標を設定し、それを達成したら顧客に報奨金を出すものです。
目標を高めに設定する場合が多いでしょう。それを達成するために顧客は、実需がなくても仕入れることになります。極端な例は、携帯電話の販売に見ることができます。その影響は2つあります。ひとつは、メーカーの売上が期末に集中することです。実需は平均化しているのに工場の操業度は大きく変動します。もうひとつは、顧客とメーカーの合計在庫が増えることです。顧客の仕入れ量を消費者の需要と勘違いして、メーカーの生産量を増やすと、顧客とメーカーの両方の在庫が増えてしまいます。
対策2:対象期間の短サイクル化
リベートを撤廃するのが最も効果的です。しかし長年の商習慣を一気に変えられない場合も多いでしょう。数量リベートを1年単位の仕入れ量で決めるのではなく、半年や四半期で決めるようにすることが対策のひとつです。また、目標数量は1点ではなく、1000個ならいくら、1500個ならいくらと多段階のほうが良いでしょう。また、仕入れ量ではなく、顧客が消費者に実際に売った売上数で決めるという方法もあるでしょう。
問題3:多段階在庫
見込み生産の商品の場合、物流で最大の問題になるのは、在庫の段階が多いことです。商品が、メーカーの本社・支店・1次卸・2次卸・小売店などを経て流通する場合です。それぞれが在庫を持っていると、それだけで在庫増加の原因になります。さらに、消費者の実需要が卸やメーカーに届かないために、需要の読み間違いによって在庫が増加します。多段階に在庫を持つ場合に在庫が増加し、在庫や操業度の変動が大きくなる現象は、「ブルウイップ効果」として知られています。(
2.1(2)参照)
対策3:VMI
メーカーがeコマースや通信販売を通して消費者に直販するのが理想です。しかし販売全部を直販にするのは困難です。商流上はメーカー・卸・小売を通して販売していても、物流上の在庫の段階を減らすことが可能です。それがVMIです。(
1.2(2)/
1.8(1)参照)VMIを進めるには、メーカー・卸・小売が、相互に物流拠点の配置と受発注の現状を認識しあうことが出発点になるでしょう。
問題4:輸送リードタイム
生産拠点と販売地点は、地理的に離れています。その間には輸送の時間がかかります。トラックなどで運搬する時間だけでなく、受発注の事務手続きなどにかかる時間や、輸送ロットをまとめるための停滞時間もかかってきます。見込み生産の商品の場合、それら輸送リードタイムが長ければながいほど、欠品防止のための在庫も増えます。極端な例が国内で生産したものを海外で販売する場合や、その逆の場合です(前節2.4(3)参照)。
国内で生産したものを国内で販売する場合にも、輸送リードタイムの長短によって必要な在庫量が変わってきます。しかしながら、必要な在庫量よりも持ちすぎている場合が多いようです。
対策4:物流拠点・生産拠点の見直しと共同物流
輸送リードタイムの短縮を検討する前に、物流拠点、生産拠点の見直しが必要です。それを検討する第一歩は、顧客が要望する納入リードタイムを明らかにすることです。納入リードタイムによって物流拠点の数が変わってきます。物流拠点が多くなればなるほど、同じ商品を複数の場所で持つために在庫量が増えます。
必要な納入リードタイムはどの位でしょうか?即納が求められるという答えが多いでしょう。しかし慣習的にそうなっている場合があります。ある会社では、午前中受注のものは午後配送、午後受注したものは翌日配送としていました。しかし受注を待っているのではなくて、曜日を決めて翌週ぶんの注文を確認するようにしたら、大半のものはそれで済むそうです。受注から納品まで中2日とれれば、全国の在庫を1個所にまとめることができます。地方に持つ在庫は、緊急用に売れ筋商品だけを少量持てば済みます。
必要な納入リードタイムが明らかになれば、必要な物流拠点の数が決まってきます。必要な物流拠点数よりも多く持ちすぎている場合が通常です。受注から納品まで中2日待てるのであれば、日本全国で必要な在庫を1個所に集中できます。午前中受注午後配送、ならば、日本全国で7~8個所になるでしょう。自動車部品は受注から数時間で納品するために、全国で200個所以上の拠点を持っているそうですが、これは最も多い部類に属するでしょう。
物流拠点を見直す場合に、卸・小売の拠点とともに見直して、VMIとするのが理想です。また生産拠点の見直しもできればベストでしょう。日本全国で7~8個所の物流拠点が必要な場合、生産拠点も同数に分散できれば、物流と生産の拠点を統合できます。
物流拠点を見直した後に、輸送リードタイムの短縮を検討します。ここで問題になるのは、トラック1台分に満たない小口輸送でしょう。その対策は、自社だけで輸送するのではなくて、他社と共同輸送することです。3PL、つまり物流会社へ委託することで、物流会社の中で他社との共同輸送を図ることも有効です。
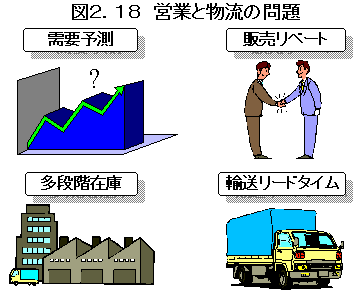